The Role of Sand in Sand Casting Types and Their Applications
Sand casting is a widely used metal casting process that involves pouring molten metal into a sand mold to create a desired shape. The quality of the final product heavily depends on the properties of the sand used in the molding process. There are several types of sand utilized in sand casting, each with its unique characteristics and advantages. This article will explore the various types of sand commonly used in sand casting, their properties, and their specific applications.
1. Green Sand
Green sand is the most commonly used type of sand in sand casting. It is a mixture of silica sand, clay, and moisture, which gives it strength and flexibility. The term green does not refer to the color but rather to the moisture content; green sand molds are not baked or cured before pouring the molten metal.
Properties - High compressive strength - Good flowability - Excellent ability to retain shape
Applications Green sand is particularly suitable for producing large castings, such as engine blocks and automotive parts. Its ability to withstand high temperatures and pressures makes it a popular choice in foundries.
2. Silica Sand
Silica sand, composed mainly of quartz, is another essential type of sand used in sand casting. It is known for its high melting point and thermal stability, which are crucial for preventing the mold from breaking down when molten metal is introduced.
Properties - High pureness (over 95% SiO2) - Excellent resistance to heat - Low expansion properties
Applications Silica sand is often used in the production of molds that require high precision and detail. It is suitable for the casting of steel, iron, and aluminum products. Its fine grains are also advantageous for creating intricate designs.
3. Oil-bonded Sands
Oil-bonded sands are a mixture of sand and a binding agent made from oil. This type of sand offers different properties compared to green sand, primarily due to the absence of moisture.
what type of sand is used in sand casting
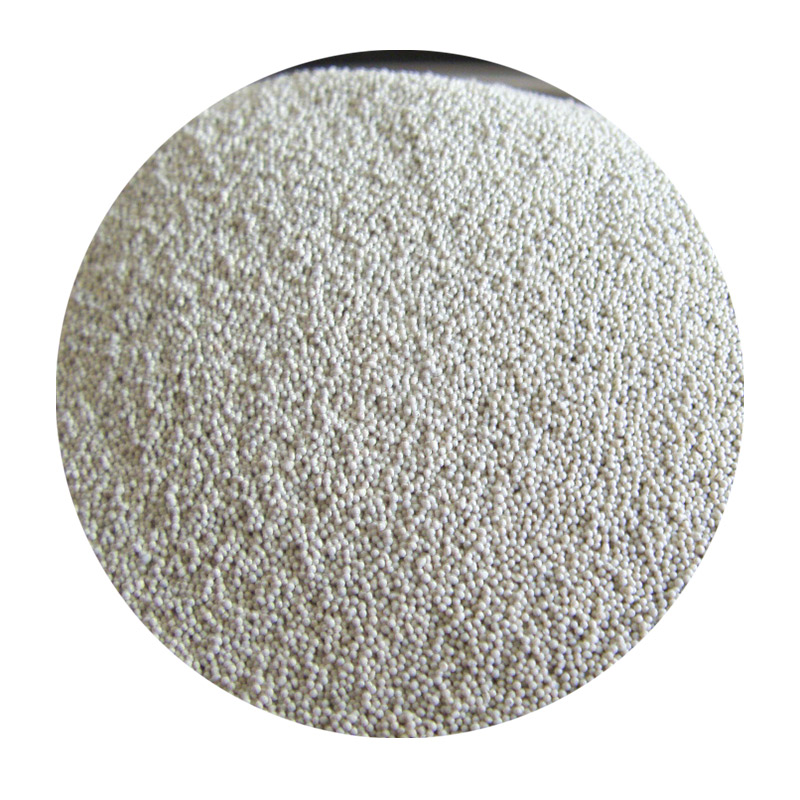
Properties - Excellent strength and durability - Better surface finish - Reduced gas porosity
Applications Oil-bonded sands are typically used for creating molds that need a high surface finish, such as artistic or intricate castings. They are suitable for applications in industries that demand precise and smooth surfaces, such as jewelry and aerospace parts.
4. Resin-bonded Sands
Resin-bonded sands consist of sand particles that are coated with a synthetic resin, which acts as a binder. This type of sand is cured with heat or chemicals to enhance mold strength.
Properties - Very high strength - Excellent dimensional stability - Smooth surface finish
Applications Resin-bonded sands are often used for the production of complex shapes and high-volume castings. They are commonly employed in foundries that focus on high-end applications, such as automotive and aerospace industries, where precision and surface quality are critical.
5. Ceramic Sands
Ceramic sands are less common but increasingly utilized for specific applications. These sands consist of high-quality ceramically engineered sand particles that can withstand extreme temperatures.
Properties - High refractoriness - Excellent thermal shock resistance - Minimal expansion during heating
Applications Ceramic sands are used in specialty casting processes, especially where extreme temperatures are involved, such as turbine blades or other components in power generation equipment. They provide superior performance in applications demanding high heat resistance.
Conclusion
The choice of sand in the sand casting process significantly influences the quality and precision of the final casting. Understanding the various types of sand—green sand, silica sand, oil-bonded sands, resin-bonded sands, and ceramic sands—enables manufacturers to select the appropriate material for their specific casting needs. Each type of sand provides unique benefits and is tailored for particular applications, making sand casting a versatile and effective manufacturing method in metalworking industries. As technology advances, the development of new sand materials and formulations continues to enhance the capabilities and applications of sand casting.
Post time:12 月 . 06, 2024 03:16
Next:wet sand 3d print