Types of Sand in Foundry
Foundries play a critical role in metalworking and manufacturing, offering processes such as casting, molding, and fabrication. One of the most essential materials in a foundry is sand, which forms the basis for molds and cores in the casting process. Different types of sand are utilized, each with its unique properties and applications. Understanding these types is crucial for optimizing casting quality and cost-effectiveness.
1. Silica Sand
Silica sand is the most common type of sand used in foundries. Composed mainly of silicon dioxide (SiO2), it has excellent properties that make it ideal for mold making. Its high melting point (around 1710°C) and ability to withstand high temperatures make it suitable for ferrous and non-ferrous metals. Silica sand can be used in both green sand and resin-bonded sand systems, providing versatility in various casting processes.
2. Green Sand
Green sand is a mixture of silica sand, clay (typically bentonite), water, and additives. As the name suggests, it is moist and used in a 'green' state without drying. This type of sand is favored for its ability to retain moisture, which aids in binding and allows for intricate mold designs. Green sand is widely employed for manufacturing iron and steel castings due to its superior moldability and cost-effectiveness.
types of sand in foundry
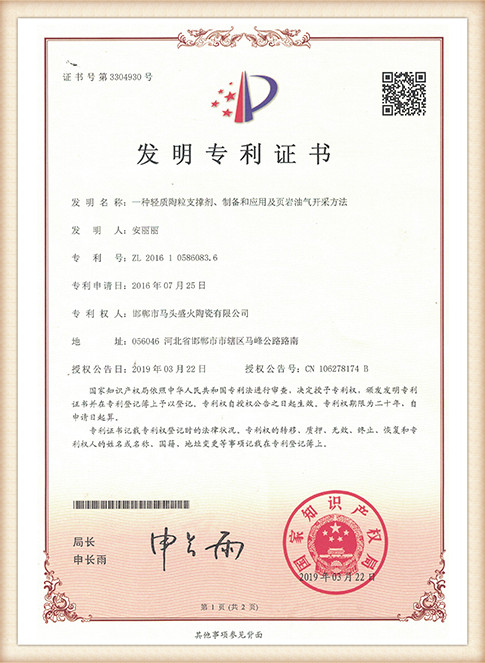
Resin-bonded sand is a modern alternative to traditional green sand. It incorporates synthetic resins as a binder, allowing for higher precision and finer details in castings. The molds formed from resin-bonded sand offer excellent surface finishes and minimal need for post-casting machining. This type of sand can withstand higher temperatures, making it suitable for high-performance applications, especially in the aerospace and automotive industries.
4. Zircon Sand
Zircon sand, derived from zirconium silicate, is known for its high melting point and excellent thermal stability. It is used in the production of molds for casting high-temperature alloys. The low thermal expansion of zircon sand minimizes the risk of defects such as cracking and distortion during cooling. Its unique properties make it a premium choice for specialized applications, although it is typically more expensive than other sand types.
5. Chromite Sand
Chromite sand, made from chromium ore, is another specialty sand used in foundry applications. It offers superior thermal conductivity and resistance to metal penetration. This type is particularly valuable for casting ferrous metals, where it can prevent sand burn-on and improve mold durability. Chromite sand's unique composition reduces the risk of oxidation and other defects, making it a preferred choice for high-performance casting applications.
Conclusion
In summary, the type of sand chosen for foundry operations significantly impacts the quality, efficiency, and cost of the casting process. From the widely used silica and green sands to specialized options like zircon and chromite sands, understanding the properties and applications of each type ensures better decision-making in foundry practices. As technology evolves, the development of new materials and sand formulations continues to expand the horizons of foundry operations, enhancing the capabilities of manufacturers worldwide.
Post time:9 月 . 21, 2024 16:17
Next:lost foam sand casting