Steel Sand Casting A Reliable Method for High-Quality Metal Parts
Steel sand casting is a time-honored manufacturing process that has been utilized for centuries in various industries, including automotive, aerospace, and machinery. This method involves pouring molten steel into a sand mold, allowing it to cool and solidify into the desired shape. Its versatility, cost-effectiveness, and ability to produce complex geometries make steel sand casting a preferred choice among many engineers and manufacturers.
One of the primary advantages of steel sand casting is its ability to produce intricate designs. The sand molds can be easily shaped to accommodate complex features, undercuts, and elaborate patterns that would be challenging to achieve using other manufacturing methods. This capability is particularly beneficial in industries where precision and detail are paramount, such as in the production of engine components or specialized machinery parts.
The process of steel sand casting begins with creating a pattern, typically made from wood or metal, that defines the shape of the final product. This pattern is then used to form a mold from a mixture of sand and binder materials. Once the mold is prepared, molten steel is poured into it, filling the cavity created by the pattern. After the steel has cooled and solidified, the mold is broken away to reveal the cast part.
steel sand casting
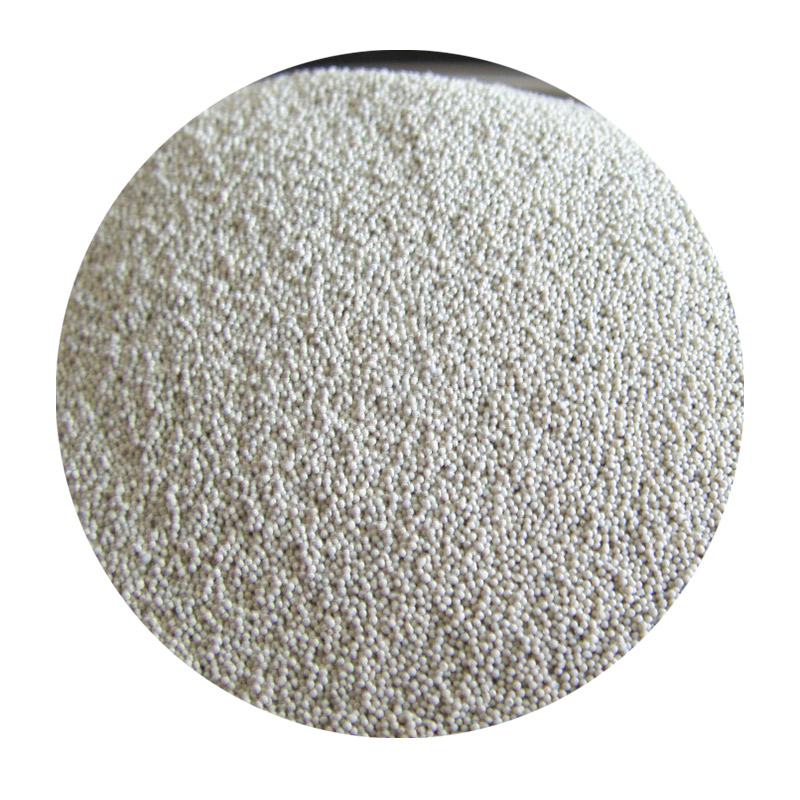
Steel sand casting is also known for its cost-effectiveness, especially in producing medium to large quantities of parts. The materials used in the sand mixture are relatively inexpensive, and the molds can often be reused for multiple casting cycles. This makes it an attractive option for manufacturers looking to keep production costs low while still achieving high-quality results. Furthermore, the process can accommodate a wide variety of steel alloys, allowing for tailored mechanical properties to meet specific application requirements.
Environmental considerations are increasingly important in modern manufacturing. Fortunately, advancements in steel sand casting methods have made the process more sustainable. For instance, the use of recyclable sand and environmentally friendly binders reduces waste and minimizes the environmental impact. Additionally, modern foundries employ various technologies to decrease energy consumption during the melting and casting processes, contributing to a greener approach to manufacturing.
Quality control is crucial in steel sand casting, as defects can significantly impact the performance of the final product. Manufacturers implement rigorous inspection protocols to ensure cast parts meet strict quality standards. Techniques such as ultrasonic testing, radiographic inspection, and dye penetrant testing are commonly used to identify and address any defects before the parts are sent to customers.
In conclusion, steel sand casting remains a vital and reliable method for producing high-quality metal parts across various industries. Its ability to accommodate complex designs, cost-effectiveness, and adaptability to different steel alloys make it an attractive option for manufacturers. As technology continues to advance, the steel sand casting process is becoming more efficient and environmentally friendly, ensuring its relevance in the modern manufacturing landscape. Whether for small-scale projects or large production runs, steel sand casting provides a lasting solution for high-performance components, making it an essential technique in the field of metalworking.
Post time:10 月 . 31, 2024 23:11
Next:Resin and Sand Blend for Durable Molds and Castings in Artistic Applications