The Intricacies of Steel Sand Casting
Steel sand casting is a widely used manufacturing process that has been pivotal in producing complex metal parts across various industries. This technique offers a blend of flexibility, efficiency, and precision, making it a popular choice in sectors such as automotive, aerospace, and machinery manufacturing.
What is Steel Sand Casting?
At its core, steel sand casting involves creating a mold from a mixture of sand and bonding agents, which is then filled with molten steel to form a desired shape upon cooling and solidifying. The process begins with designing a pattern, typically made of metal or plastic, which resembles the final product. The pattern is placed in a sand mold, and the space around it is packed tightly with a sand mixture. Once the mold is prepared, it is ready to receive molten steel, which can reach temperatures exceeding 1500 degrees Celsius.
Advantages of Steel Sand Casting
One of the most significant advantages of steel sand casting is its versatility. This method can accommodate a wide range of steel alloys, including carbon steel, alloy steel, and stainless steel, allowing for the creation of parts suited for various applications. Additionally, sand casting is ideal for producing large components, with weights ranging from a few grams to several tons, making it suitable for heavy machinery and infrastructure.
Another notable benefit is the cost-effectiveness of the process. The materials used in sand molds are relatively inexpensive, and the ability to recycle sand for multiple uses further enhances its economic appeal. Moreover, the process allows for intricate designs and complex geometries that might be difficult or impossible to achieve with other manufacturing methods. This flexibility not only aids in design innovation but also ensures that manufacturers can adapt to the changing needs of the market.
steel sand casting
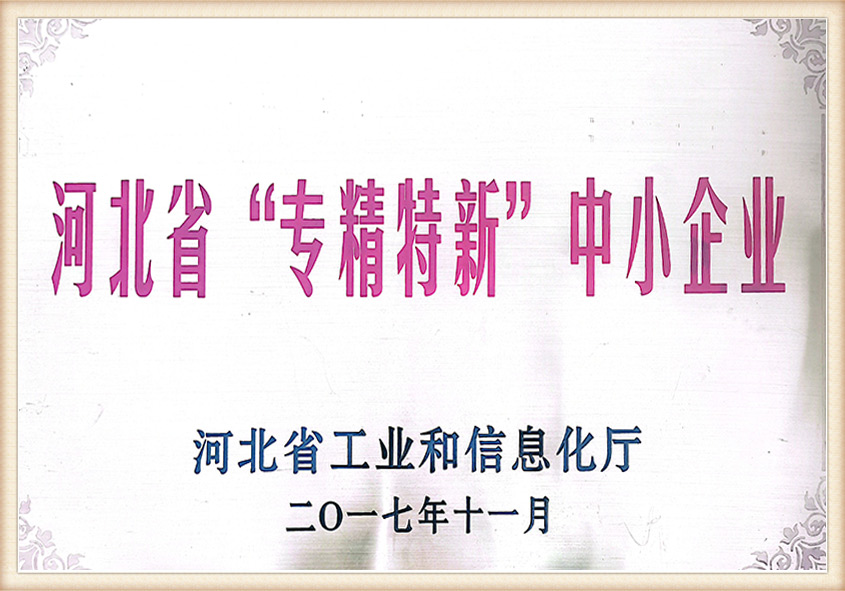
Applications of Steel Sand Casting
Steel sand casting finds applications in various industries. In the automotive sector, it is commonly used to produce engine blocks, transmission cases, and various structural components. In aerospace, cast steel parts such as landing gear components and structural frames are manufactured to meet the stringent safety and performance standards required. Additionally, the machinery industry utilizes sand casting for producing gearboxes, pump housings, and many other essential components.
The Casting Process
The steel sand casting process can be broken down into several key steps pattern making, mold making, pouring, cooling, and finishing. After the mold is created, molten steel is poured into it, filling the cavity left by the pattern. The cooling time depends on the size and complexity of the casting, after which the mold is broken away to reveal the finished product. The last stage involves cleaning, trimming, and any necessary machining to achieve the required surface finish and dimensional accuracy.
Conclusion
Steel sand casting is a time-honored technique that continues to thrive in modern manufacturing. Its ability to produce high-quality, intricate components at a reasonable cost positions it as a crucial player in the industry. As technology advances and the demand for innovation in metal production escalates, steel sand casting will undoubtedly evolve, embracing new methodologies and materials to meet the challenges of tomorrow’s manufacturing landscape.
Post time:10 月 . 10, 2024 22:39
Next:resin sanding