The Art and Science of Stainless Steel Sand Casting in Foundries
Stainless steel sand casting is a vital manufacturing process in various industries, ranging from automotive to aerospace, and even in architecture. This technique combines the durability of stainless steel with the molding abilities of sand, resulting in high-quality castings that meet rigorous industry standards. By understanding the intricacies of stainless steel sand casting foundries, we can appreciate the craftsmanship involved in creating complex components.
What is Stainless Steel Sand Casting?
At its core, stainless steel sand casting involves pouring molten stainless steel into a mold made from sand. The sand is typically mixed with a binder to ensure that it holds its shape during the pouring process. Once the molten metal is introduced, it fills the mold cavity, taking on its form as it cools and solidifies. After cooling, the sand mold is broken away, revealing the cast stainless steel product.
Advantages of Sand Casting
One of the main advantages of sand casting is its versatility. This process can produce parts of various sizes and shapes, from small intricate designs to large components weighing several tons. Moreover, the setup costs for sand casting are relatively low compared to other casting methods, making it an attractive option for low to medium volume production. This flexibility allows manufacturers to achieve complex geometries that might be difficult or impossible with other casting techniques.
Another significant benefit of using stainless steel is its resistance to corrosion, heat, and mechanical stress. These properties make it ideal for components used in harsh environments, such as marine applications, chemical processing, and food processing equipment. Additionally, stainless steel offers a polished finish that is aesthetically pleasing and easy to clean, further enhancing its suitability for various applications.
The Process Flow
stainless steel sand casting foundry
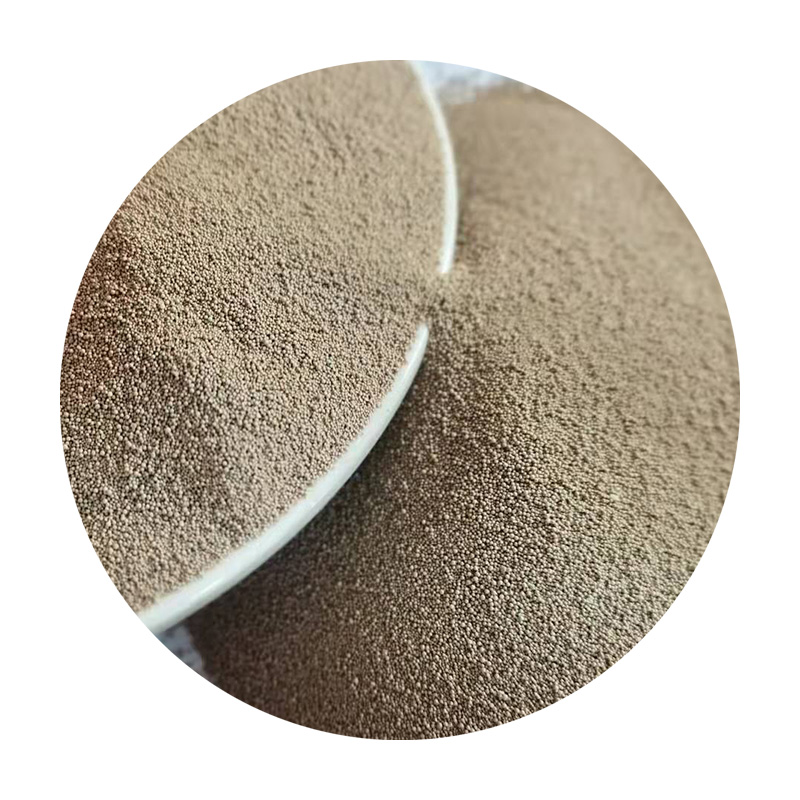
The sand casting process begins with pattern making. A pattern is a replica of the desired part, usually made from materials like wood or metal. It is crucial for the pattern to accurately represent the final product, taking into account factors such as shrinkage during cooling and dimensional tolerances.
Once the pattern is created, the next step is molding. Foundry workers prepare the sand mixture, which typically consists of silica sand, clay, and water. They pack this sand around the pattern to create a mold. Once the mold is set, the pattern is removed, leaving a cavity in the sand.
With the mold ready, the foundry heats the stainless steel until it reaches a molten state, usually around 1400-1500 degrees Celsius. The molten steel is then poured into the mold through a gating system that controls the flow and ensures proper filling. After the steel cools and solidifies, the sand mold is broken away, and the final casting is cleaned and inspected for defects.
Quality Control and Finishing
Quality control is a critical aspect of stainless steel sand casting. Foundries often employ various testing methods to ensure the integrity of the castings, including nondestructive testing (NDT) to detect internal flaws. Additionally, surface finishing processes such as grinding, polishing, or shot blasting are used to achieve the desired surface quality.
Conclusion
Stainless steel sand casting foundries play a crucial role in producing high-quality, durable components that meet the demands of modern industries. By leveraging the unique properties of stainless steel and the versatility of sand casting, manufacturers can create intricate designs that are resistant to corrosion and wear. As technology advances, the methods and materials used in these foundries will continue to evolve, further enhancing the quality and efficiency of stainless steel casting. This age-old process marries art and science, ensuring that the components produced can withstand the test of time and serve a multitude of applications across the globe.
Post time:10 月 . 06, 2024 03:21
Next:can you sand a 3d print