Sand casting is one of the most versatile and widely used manufacturing processes in the foundry industry. This technique involves creating a mold from compacted sand to produce metal parts with complex geometries. It is especially favored for its cost-effectiveness, ability to produce large and small volumes, and suitability for a variety of metals, making it essential across numerous sectors, including automotive, aerospace, and general engineering.
The sand casting process begins with the preparation of the mold. This involves mixing silica sand with a bonding agent, typically clay, and water to create a pliable mixture. The mixture is then packed around a pattern, which is usually a replica of the final product. The pattern can be made from various materials such as metal, wood, or plastic. Once the mold is formed, the pattern is removed, leaving a cavity that retains the shape of the desired part.
.
After the mold is prepared, molten metal is poured into the cavity. The choice of metal is crucial, as different metals have varying melting points and properties. Common metals used in sand casting include aluminum, iron, and bronze. Once the molten metal solidifies, the mold is broken away to reveal the cast part. This stage requires careful handling to prevent damage to the newly formed item.
sand casting processes
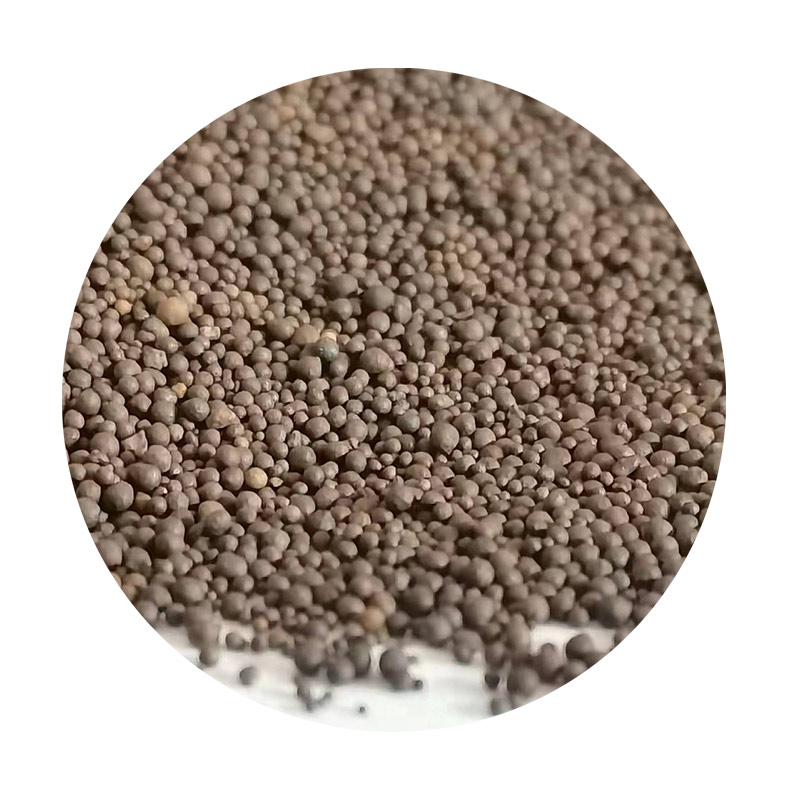
Post-casting operations often include processes such as machining, sanding, and surface finishing to achieve the desired product specifications. These subsequent steps are vital for improving surface quality and dimensional accuracy. Additional treatments may also be applied, such as heat treatment, to enhance the mechanical properties of the cast metal.
Despite the advantages, sand casting does have its challenges. The quality of the sand and the skill of the operators play significant roles in the outcome of the casting. Issues such as sand contamination, defects in the mold, or improper pouring can lead to imperfections in the final product. Moreover, the process is generally slower than other casting methods like die casting, which may not be ideal for high-volume production runs.
In conclusion, sand casting remains a crucial process in manufacturing due to its adaptability and effectiveness in producing complex metal parts. As industries evolve and technological advancements occur, the sand casting process continues to improve, positioning itself as a reliable and cost-efficient method for a wide range of applications. Its enduring relevance highlights the importance of understanding traditional manufacturing processes in an increasingly automated and digital world.
Post time:11 月 . 01, 2024 18:20
Next:Techniques for Smoothing and Finishing Resin 3D Prints Effectively and Efficiently