Understanding Sand Casting A Comprehensive Overview
Sand casting, also known as sand mold casting, is a versatile and widely used manufacturing process that has been employed for centuries. It is particularly valued for its ability to produce complex shapes and large parts with relative ease and cost-effectiveness. This article explores the intricacies of the sand casting process, its advantages, applications, and key considerations.
The Sand Casting Process
At its core, sand casting involves creating a mold from a sand mixture, which is then filled with molten metal to form a desired object. The process can be broken down into several key steps
1. Pattern Creation The first step in sand casting is to create a pattern, which is a replica of the final product. Patterns can be made from various materials, such as wood, metal, or plastic, and they are designed slightly larger than the final object to account for metal shrinkage during cooling.
2. Mold Preparation The pattern is placed in a specially prepared sand mixture, often consisting of silica sand, clay, and water. This mixture is compacted around the pattern to create a mold. Once the mold is set, the pattern is carefully removed, leaving a cavity that reflects the shape of the desired part.
3. Pouring After preparing the mold, the molten metal, heated to its liquefying point, is poured into the cavity. The metal fills the void left by the pattern, taking on its shape.
4. Cooling and Solidification The molten metal is allowed to cool and solidify within the mold. This process can vary in duration depending on the size of the casting and the type of metal being used.
5. Mold Removal and Finishing Once the metal has cooled and hardened, the sand mold is broken away, leaving the cast part. At this stage, any excess material, known as flashing, is removed, and the surface may undergo finishing processes such as grinding or polishing to achieve the desired tolerance and surface finish.
Advantages of Sand Casting
sand casting description
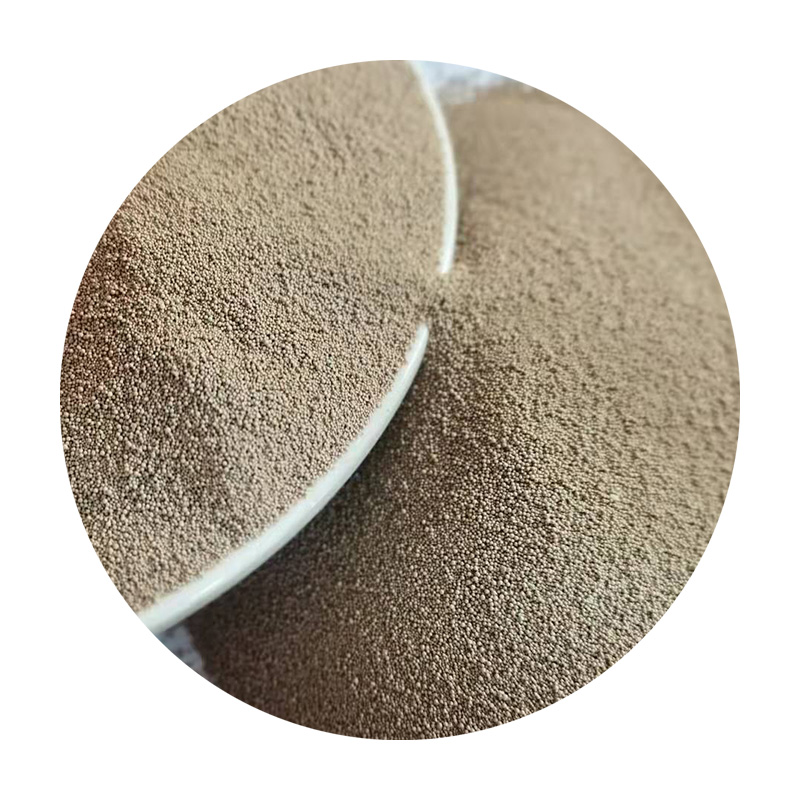
One of the most significant advantages of sand casting is its adaptability. The process is capable of producing intricate shapes with high precision, making it suitable for a multitude of applications in industries such as automotive, aerospace, and manufacturing. Moreover, the materials used in sand casting are generally abundant and inexpensive, resulting in a lower production cost compared to other casting methods.
Another benefit is the ability to work with various metals, including iron, steel, aluminum, bronze, and magnesium. This flexibility allows for a wide range of properties in the finished product, catering to different engineering requirements.
Applications
Sand casting is employed in numerous applications, from small-scale projects to large industrial components. Common products include engine blocks, pipe fittings, and various machine parts. The method is particularly favored in industries requiring low to medium production volumes where the complexity of parts may make other methods less feasible.
Key Considerations
While sand casting offers numerous advantages, some challenges must be considered. The quality of the casting can be affected by factors such as sand quality, moisture content, and pouring temperature. Proper control and monitoring of these parameters are crucial for achieving consistent and quality results.
In addition, sand casting may not be the best choice for high-precision components as the surface finish may not always meet stringent tolerances without additional machining. However, advancements in technology, such as 3D printing of sand molds, are continuously improving the capabilities and applications of this traditional casting method.
Conclusion
In summary, sand casting is a time-honored manufacturing process that remains relevant in modern production due to its flexibility, cost-effectiveness, and ability to produce complex shapes. Understanding the intricacies of this process enables manufacturers to harness its full potential, ensuring high-quality output in a diverse range of applications. As technology continues to evolve, the future of sand casting looks promising, potentially expanding its applications even further in the industrial landscape.
Post time:10 月 . 10, 2024 23:51
Next:Exploring the Benefits and Techniques of Sand Castings in Manufacturing Processes