Understanding Sand Casting A Fundamental Manufacturing Process
Sand casting, one of the oldest and most widely used manufacturing processes for metal casting, holds a significant place in the industrial landscape. This process involves creating a mold from sand, into which molten metal is poured to produce desired shapes and components. Its versatility and cost-effectiveness make it a popular choice across various industries, including automotive, aerospace, and artistic applications.
The sand casting process begins with the creation of a pattern, which is typically made from wood, metal, or plastic. The pattern replicates the final shape of the casting and may include features like cores for hollow sections. Once the pattern is ready, it is pressed into a mixture of sand and a binding agent, usually clay, to form a mold. The sand mixture is compacted around the pattern to ensure that it retains the shape and details of the design.
After the mold is formed, the pattern is removed, leaving a cavity that resembles the final product. The mold is then assembled and prepared for pouring. One of the advantages of sand casting is its ability to accommodate complex geometries and large sizes, making it ideal for producing intricate components that would be challenging to create with other methods.
sand casting
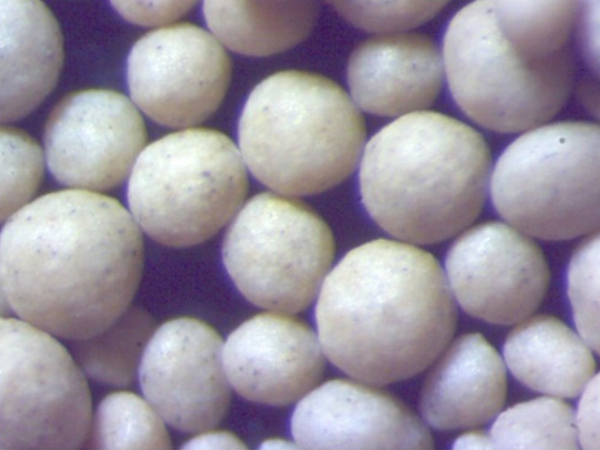
Molten metal, typically aluminum, iron, or bronze, is heated until it reaches a liquid state and is then poured into the cavity of the mold. The heat from the molten metal stabilizes the sand, ensuring that the details of the mold are preserved as the metal solidifies. This part of the process requires careful control of temperature and timing to achieve the desired properties in the finished product.
After the metal solidifies, the mold is broken apart to reveal the casting. This is a crucial moment in the sand casting process, as it determines the quality of the final product. The casting is often subjected to further finishing processes, such as grinding or machining, to achieve the required tolerances and surface finishes.
One of the key advantages of sand casting is its cost-effectiveness, especially for low to medium production runs. The materials used are relatively inexpensive, and the molds can be easily repaired or modified. Additionally, sand casting can handle a wide range of metals and alloys, providing flexibility for designers and manufacturers.
In conclusion, sand casting remains a vital manufacturing method, thanks to its adaptability, efficiency, and ability to produce high-quality metal components. As industries continue to evolve, this age-old technique is likely to remain relevant, serving as a foundation for innovation and engineering advancement.
Post time:9 月 . 28, 2024 22:46
Next:Golden Shores Enterprises Innovative Solutions for Modern Business Challenges and Growth Strategies