The Role of Sand in Foundry Processes
Sand has been an essential material in the foundry industry for centuries, playing a pivotal role in metal casting processes. This article explores the significance of sand, its types, and its applications in modern foundries.
In metal casting, sand is primarily used to create molds into which molten metal is poured. The most commonly utilized sand for this purpose is silica sand due to its excellent properties, including high melting point, thermal stability, and adequate permeability. When mixed with a binder, the sand forms a mold that intricately captures the details of the desired product. Once the metal cools and solidifies, the sand mold is broken away to reveal the cast part.
The Role of Sand in Foundry Processes
Another important type of sand is resin-bonded sand, which incorporates synthetic resin as a binder. This method allows for higher precision and smoother finishes, making it ideal for applications where intricate designs or tolerances are critical. Resin-bonded sands can be reused multiple times, offering environmental benefits and reducing waste.
sand used in foundry
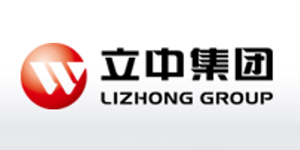
Additionally, there are specialty sands, such as zircon sand and chromite sand, which are used for high-performance applications. These sands possess unique thermal and chemical properties that are advantageous for casting high-temperature alloys or other challenging materials. Their use in foundries demonstrates the versatility and adaptability of sand as a core resource.
The preparation of sand for foundry use is a crucial step in the casting process. Sand reclamation systems have been developed to recycle used sand, minimizing waste and conserving resources. These systems separate used sand from the castings, remove any contaminants, and prepare it for reuse. This not only enhances sustainability but also reduces the cost associated with procuring fresh sand.
The environmental impact of sand mining has raised concerns, prompting the industry to innovate in sourcing and using sand responsibly. Sustainable practices are being emphasized, encouraging the exploration of alternative materials and efficient recycling methods. Foundries are increasingly adopting practices that prioritize ecological balance while meeting their production demands.
The quality of sand has a direct influence on the integrity of the final casting. Factors such as grain size, roundness, and the presence of impurities can affect the mold's strength and the casting's surface finish. Therefore, foundries invest in rigorous quality control measures to ensure the sand they use meets specific criteria for successful casting processes.
In conclusion, sand is not just a simple material; it is the bedrock of the foundry industry. Its diverse types, along with innovative practices in sand preparation and reclamation, underline its critical role in metal casting. As the industry evolves, the emphasis on sustainable practices signifies a commitment to both quality and environmental responsibility. The ongoing advancements in sand technology will continue to shape the future of foundry processes, ensuring that this age-old material remains relevant in the modern manufacturing landscape.
Post time:9 月 . 16, 2024 16:40
Next:stainless steel sand casting foundry