Physical Properties of Foundry Sand
Foundry sand is a crucial material in metal casting processes, where it is primarily used to form molds and cores for various metal parts. The physical properties of foundry sand play a significant role in determining the quality of the final cast product. Understanding these properties is essential for foundry engineers and operators to optimize the casting process and ensure efficiency.
One of the primary physical properties of foundry sand is its grain size distribution. The size of sand grains affects the mold’s permeability, compaction, and surface finish of the casted product. Generally, foundry sands are graded based on their particle size, which is typically measured in millimeters or micrometers. A specific grain size can enhance the mold's ability to allow gases to escape during pouring, thus reducing defects such as gas porosity in the final product. Fine sands provide smooth surfaces but may have lower permeability, while coarser sands improve air flow but can lead to rougher surfaces.
Another important physical property is the shape of the sand grains. Sand that consists of angular grains tends to interlock better, which increases mold strength. In contrast, rounded grains are generally easier to handle and can help in forming smooth surfaces. The balance between these two types is crucial for achieving the desired mold strength while maintaining ease of use. Foundries often utilize a mix of grain shapes to attain optimal performance.
physical properties of foundry sand
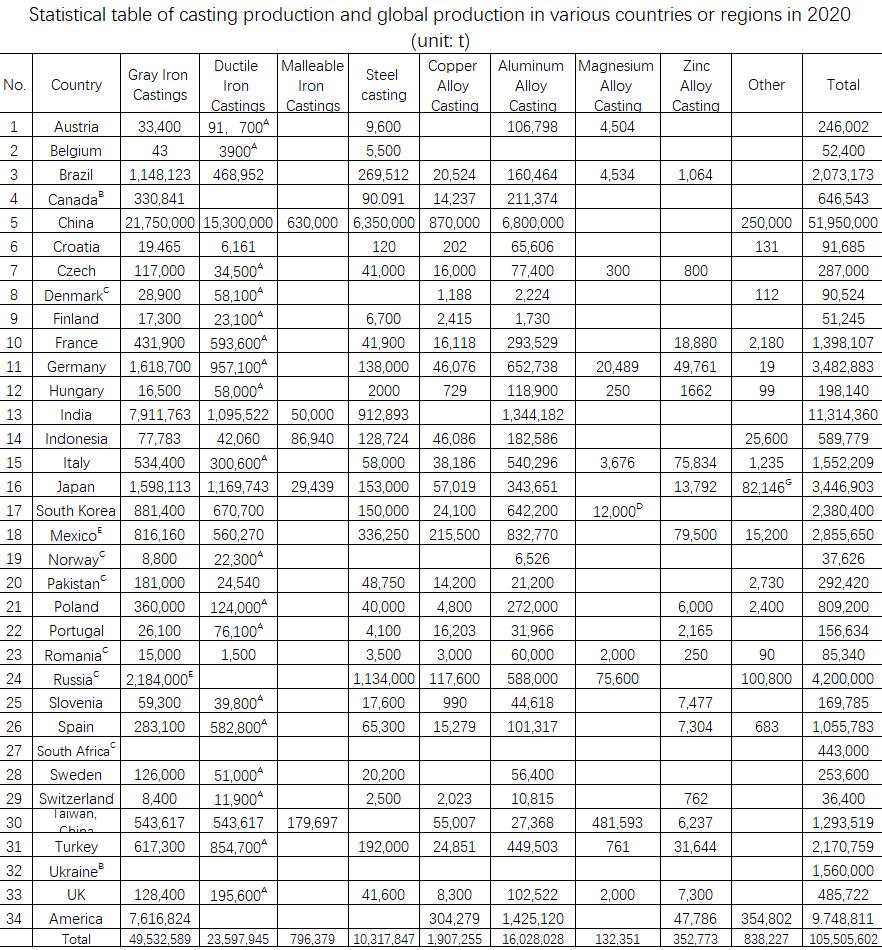
Moisture content is also a vital characteristic of foundry sand. The amount of water present in the sand mixture can significantly impact its molding properties. Too much moisture can lead to defects such as steam explosions, while too little can result in poor mold cohesion and strength. Foundries typically control the moisture content to maintain an optimal balance, usually between 2% to 5%. This control is vital for the overall quality of the mold and the resulting cast product.
Bonding agents, such as clay and resins, further influence the physical properties of foundry sand. Clay, commonly used in green sand molding, serves as a binder, providing the necessary strength and plasticity to the mixture. The type and amount of binding agent directly affect the thermal properties of the sand, which are critical during casting as they need to withstand high temperatures without breaking down.
Finally, thermal conductivity is another significant property of foundry sand. A sand’s ability to conduct heat affects the cooling rate of the molten metal and ultimately influences the final crystalline structure of the cast product. High thermal conductivity can lead to faster heat dissipation, which may require adjustments to the casting process to achieve the desired metallurgical properties.
In conclusion, the physical properties of foundry sand, including grain size distribution, grain shape, moisture content, bonding agents, and thermal conductivity, collectively determine the quality and efficiency of metal casting processes. By carefully managing these properties, foundries can enhance mold performance, reduce defects, and improve the overall outcomes of their casting operations. Understanding these parameters allows foundry professionals to choose the right type of sand and tailor their processes for optimal results.
Post time:10 月 . 03, 2024 08:51
Next:Effective Techniques for Sanding Stainless Steel Surfaces Smoothly and Efficiently