Lost Foam Casting Method A Comprehensive Overview
Lost foam casting is an innovative metal casting technique that has gained significant popularity in recent years. This method merges traditional casting practices with modern technology, providing a unique approach that offers several advantages over conventional casting methods. In this article, we will explore the principles of lost foam casting, its process, benefits, applications, and future prospects.
Principles of Lost Foam Casting
The lost foam casting method is a type of evaporative pattern casting, which utilizes a foam pattern made usually from expanded polystyrene (EPS) or other foam materials. The key principle behind this technique lies in the fact that the foam pattern is not removed from the mold but instead is allowed to evaporate during the casting process. This technique was initially developed for producing cast iron and has since been adapted for a variety of metals, including aluminum and bronze.
The Lost Foam Casting Process
The lost foam casting process can be broken down into several key steps
1. Pattern Creation A foam pattern is created according to the specifications of the desired final product. This pattern is lightweight and can be shaped into complex geometries that would be difficult to achieve with traditional metal patterns.
2. Coating The foam pattern is then coated with a refractory material, typically a mixture of sand and a binding agent. This coating not only supports the pattern during the casting process but also creates a boundary that defines the shape of the final cast product.
3. Molding The coated foam pattern is placed in a mold box, which is filled with more sand to create a complete mold around the pattern. The sand is compacted around the coated pattern to ensure it maintains its shape during the casting process.
4. Pouring Once the mold is prepared, molten metal is poured into the mold. The heat from the metal causes the foam pattern to evaporate almost instantaneously, allowing the molten metal to take its place and fill the cavity.
5. Cooling After the metal has been poured, it is allowed to cool and solidify. Once solidification is complete, the sand mold is broken away, revealing the final cast part.
lost foam casting method
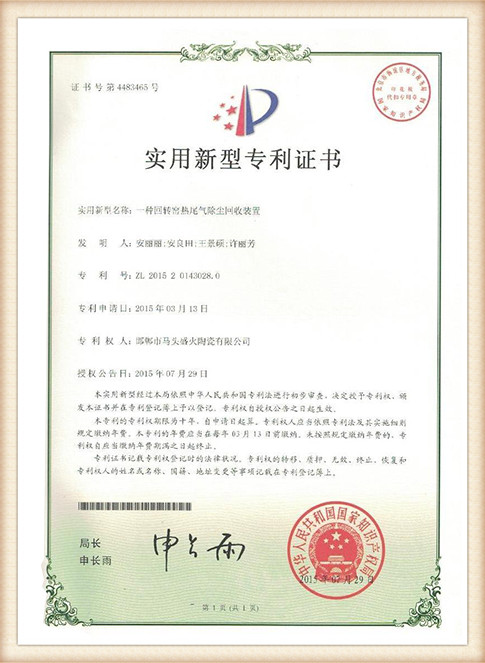
Benefits of Lost Foam Casting
Lost foam casting offers several advantages compared to traditional casting methods.
- Design Flexibility One of the most significant benefits is its ability to produce intricate designs and complex shapes that may not be feasible with conventional methods. This flexibility makes it an excellent choice for industries requiring precise and detailed components.
- Reduced Waste Since the foam pattern evaporates, there is minimal waste generated during the process, making it a more environmentally friendly option. Traditional casting often requires additional steps to remove patterns, leading to increased waste.
- Lower Production Costs Although the initial setup cost for lost foam casting can be higher due to foam pattern production, the overall production costs are often lower. The reduction in rework and waste, along with the speed of production, contributes to overall savings.
- Better Surface Finish The nature of the foam pattern allows for a smoother surface finish on the cast piece, reducing the need for extensive machining or finishing processes after casting.
Applications of Lost Foam Casting
Lost foam casting is used in various industries, including automotive, aerospace, and art casting. In the automotive sector, it is employed to produce components like engine blocks and transmission casings, where precision and weight savings are crucial. The aerospace industry benefits from this method for its ability to create lightweight, intricate parts that adhere to stringent safety and performance standards.
Future Prospects
The future of lost foam casting looks promising, especially with advancements in materials science and casting technology. Researchers continue to explore new materials for foam patterns, enhancing the properties of the casting process. As industries increasingly emphasize sustainability, lost foam casting is likely to gain further traction due to its low waste generation and efficient use of resources.
In conclusion, lost foam casting represents a significant advancement in the metal casting industry. Its unique processes, coupled with distinct advantages, make it a favorable choice for manufacturers looking to innovate and optimize their production capabilities. As technology progresses, we anticipate even broader applications and refinements in this versatile casting method.
Post time:10 月 . 17, 2024 16:18
Next:Golden Sands Community Initiative for Sustainable Development and Empowerment