High Volume Sand Casting An Overview
Sand casting, a process that has stood the test of time, remains a cornerstone in the metal casting industry. It is particularly known for its efficiency in producing high volumes of complex shapes and sizes. This article delves into the intricacies of high volume sand casting, its advantages, applications, and the factors influencing its widespread use.
At its core, sand casting involves creating a mold from sand and pouring molten metal into it to produce a desired shape. The two-part mold is made from a mixture of sand, clay, and water that is packed tightly around a pattern of the object to be cast. The pattern is removed after the sand has set, leaving an impression that is filled with molten metal. This method is exceptionally versatile and can cater to various metals, including aluminum, iron, and copper alloys.
One of the primary advantages of high volume sand casting is its cost-effectiveness, especially when producing large quantities of parts. The reusable nature of sand molds means that manufacturers can achieve economies of scale that are simply unattainable with other methods, such as die casting or investment casting. Additionally, the ability to create large and complex geometries with minimal tooling costs makes sand casting an attractive option for many industries.
high volume sand casting
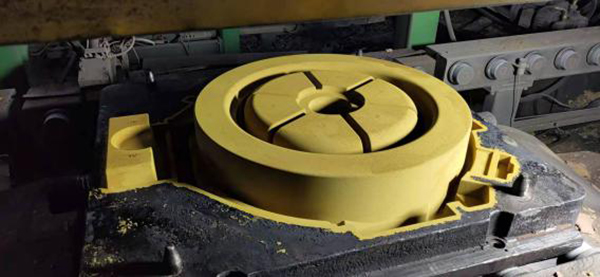
High volume sand casting finds applications across a multitude of sectors, including automotive, aerospace, and heavy machinery. Components such as engine blocks, gear housings, and other structural parts are often manufactured using this technique. The automotive industry, in particular, benefits from the speed and efficiency of sand casting, enabling the rapid production of essential parts that meet stringent quality standards.
Despite its many benefits, there are factors that influence the effectiveness of high volume sand casting. The quality of the sand, the precision of the mold-making process, and the control of pouring temperatures are all critical elements that can affect the final product. Manufacturers must also be mindful of potential defects, such as sand inclusions or surface roughness, which can compromise the integrity of the castings.
Moreover, advancements in technology have further enhanced the capabilities of high volume sand casting. Innovations such as computer-aided design (CAD), 3D printing of molds, and automated pouring systems have streamlined the process, leading to improved accuracy and reduced lead times. These technological advancements not only enhance production efficiency but also allow for more intricate designs, expanding the possibilities for manufacturers.
In conclusion, high volume sand casting is a highly effective manufacturing process that continues to evolve with technological advancements. Its cost-effectiveness, versatility, and ability to produce complex parts in large quantities make it indispensable in various industries. As manufacturers embrace new technologies and methodologies, the future of sand casting looks promising, ensuring its relevance in an ever-changing marketplace. Whether it’s for automotive components or aerospace parts, high volume sand casting remains a formidable player in metal casting today.
Post time:10 月 . 16, 2024 02:02
Next:Resin Coated Sand Suppliers for High-Quality Foundry Solutions and Services