Foundry Sand Properties An Essential Aspect of Casting Processes
Foundry sand plays a pivotal role in the metal casting industry, serving as a critical component in the creation of complex metal parts through various casting methods. This article delves into the key properties of foundry sand, its types, and its importance in ensuring high-quality castings.
Types of Foundry Sand
The most commonly used foundry sands are silica sand, clay, and synthetic sands
.1. Silica Sand This is the most prevalent type of sand used in casting processes due to its superior properties. Silica sand consists mainly of silicon dioxide (SiO2) and is known for its high melting point, which makes it suitable for metal casting. It has excellent refractoriness, thermal stability, and good permeability, allowing molten metal to flow through it without significant hindrance.
2. Clay Bonded Sand This type of sand combines silica with clay, which acts as a binding agent. Commonly used in the production of molds and cores, clay bonding provides strength and plasticity to the sand mixture. When water is added, it activates the clay, producing a pliable consistency that can be easily shaped and molded.
3. Synthetic Sand With advances in technology, synthetic sands have emerged as viable alternatives to natural sands. These are engineered materials designed to closely mimic the properties of traditional foundry sands while offering better performance and environmental benefits. Synthetic sands often have more consistent grain size, improved thermal properties, and reduced impurities.
Key Properties of Foundry Sand
The effectiveness of foundry sand in casting applications is primarily determined by several crucial properties
foundry sand properties
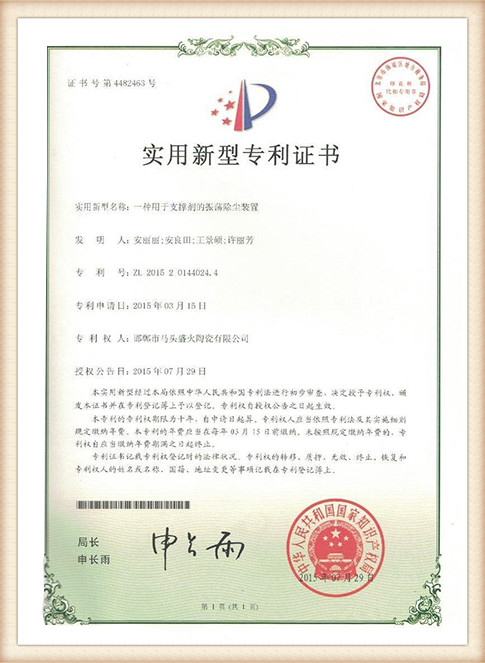
1. Grain Size and Distribution The size and shape of sand grains significantly affect the mold's permeability, strength, and the quality of the final casting. A well-graded sand mixture with a balanced distribution of grain sizes can minimize defects and ensure a smoother surface finish.
2. Permeability This property refers to the ability of the sand to allow gases and air to escape during the pouring of molten metal. Proper permeability is essential to avoid gas entrapment, which can lead to casting defects such as blowholes. Silica sand typically exhibits good permeability, making it highly desirable in the casting process.
3. Bonding Strength The strength of the sand mix is critical. It should possess enough strength to hold its shape during the casting process while still being easily removable after the metal cools. Clay-bonded sands offer excellent bonding strength, which is necessary for creating stable molds.
4. Thermal Properties Foundry sands should withstand high temperatures without breaking down or affecting the quality of the casting. High refractoriness ensures that the sand can endure extensive heat, which is especially important when working with ferrous metals.
5. Plasticity The ability of sand to be easily shaped and molded is vital for crafting intricate designs. This property allows for smooth contours and accurate dimensions in the final product, which is essential for components that require precise specifications.
6. Reusability One of the significant advantages of foundry sand, especially silica sand, is its reusability. After the casting process, the sand can be reclaimed, cleaned, and reused for subsequent molds, thus reducing material waste and lowering production costs.
Conclusion
The properties of foundry sand play an indispensable role in the quality and efficiency of the metal casting process. Understanding these properties allows foundry engineers to select the appropriate sand for specific applications, optimize mold design, and improve the overall quality of castings. As the metal casting industry continues to evolve, ongoing research and development into new types of foundry sands and their properties will be crucial in addressing production challenges while enhancing sustainability and performance. Thus, foundry sand remains a fundamental element in the successful production of high-quality metal components.
Post time:12 月 . 03, 2024 14:41
Next:Current Trends in Gold and Sand Prices for Market Investors