The Foundry Sand Casting Process A Comprehensive Overview
The foundry sand casting process is one of the oldest and most versatile metal casting techniques used in manufacturing. It involves creating a mold from sand, which is then used to shape molten metal into desired forms. This manufacturing method has been widely adopted due to its economic viability, ability to produce complex shapes, and suitability for a variety of metals, including iron, aluminum, and bronze.
History and Evolution
The roots of sand casting can be traced back thousands of years, with evidence of its usage in ancient civilizations such as Egypt and China. Over the years, advancements in materials and technology have refined the process. Today, sand casting remains a preferred method for producing large quantities of castings, particularly in the automotive and aerospace industries.
Process Overview
The sand casting process comprises several critical steps
1. Pattern Making The first step involves creating a pattern of the object to be cast. Patterns are typically made from wood, metal, or plastic and are designed slightly larger than the final product to allow for shrinkage. The pattern needs to include features like draft angles to ensure easy removal from the sand mold.
2. Mold Creation Once the pattern is ready, it is used to form the mold. This is done by packing sand around the pattern in a two-part mold or a single drag (bottom half) and cope (top half) setup. The sand is mixed with a binder, typically clay and water or chemical binders, to enhance its strength and cohesion. After the sand is compacted, the pattern is removed, leaving a hollow cavity that mirrors the desired shape.
3. Core Making (if needed) For objects with internal features, cores may be required. Cores are made from a similar sand mixture and are placed in the mold to create these internal cavities.
foundry sand casting process
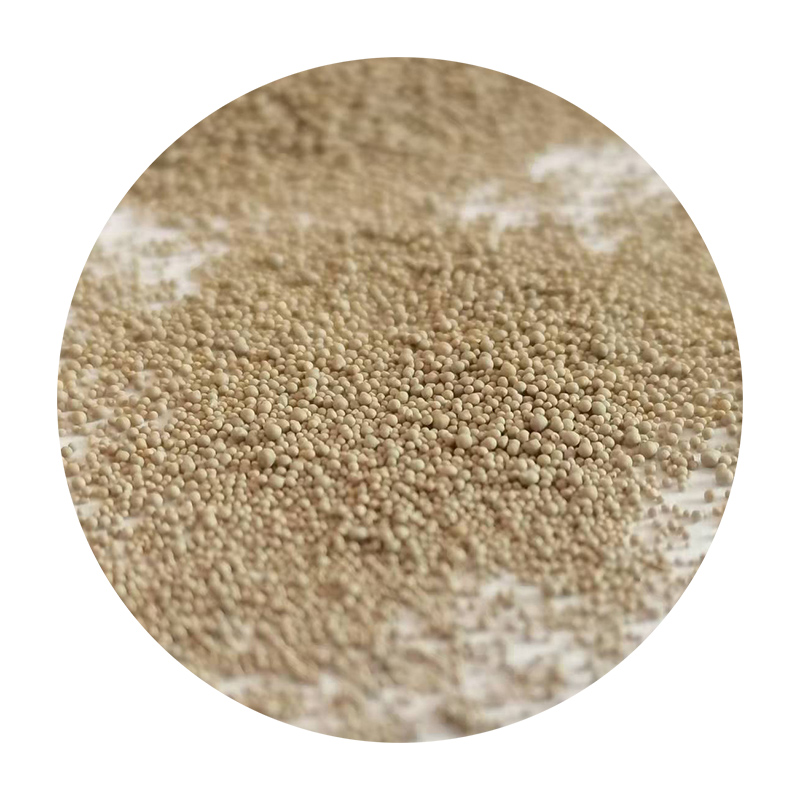
4. Melting and Pouring The metal chosen for casting is then heated until it reaches its molten state. This melting process usually takes place in a furnace. Once the metal is ready, it is poured into the sand mold through a gate system, allowing it to fill the cavity and take the shape of the pattern.
5. Cooling After the mold is filled, the molten metal is allowed to cool and solidify. The cooling time depends on the size and complexity of the casting. Once solidified, the mold can be broken away, revealing the cast object.
6. Finishing The final step in the foundry sand casting process involves cleaning and finishing the cast product. This might include removing any excess sand, trimming, grinding, or machining to achieve the desired surface finish and dimensions.
Advantages and Limitations
The foundry sand casting process offers several advantages. It is relatively low cost and can produce large and complex parts. Sand molds can be reused, and the method allows for the casting of various metals and alloys. Additionally, due to the adaptability of the sand, intricate designs can be achieved with relative ease.
However, sand casting does have its limitations. The surface finish of cast products is generally not as smooth as that achieved through other methods, such as die casting. Sand molds can also be less durable than permanent molds, leading to additional investment in mold production for large series production runs. Additionally, the process may involve more extensive finishing work to meet specific tolerances.
Conclusion
In conclusion, the foundry sand casting process remains a fundamental and widely used technique in manufacturing. Its long history speaks to its reliability and effectiveness, and ongoing innovations continue to enhance the quality and efficiency of the process. By understanding the steps and considerations involved in sand casting, manufacturers can better leverage this method to produce high-quality metal components, ensuring its place in modern manufacturing practices for years to come.
Post time:12 月 . 03, 2024 17:43
Next:super sand g2