The Foundry Sand Casting Process An Overview
The foundry sand casting process is one of the oldest and most widely used manufacturing techniques for producing complex metal parts
. It involves pouring molten metal into a sand-based mold to create a variety of components used in numerous industries, from automotive to aerospace and beyond.The process begins with the creation of a mold, which is typically made from a mixture of sand, a bonding agent, and other additives. This mixture is compacted into a two-part mold, consisting of the cope (top half) and the drag (bottom half). The sand's grain size, shape, and distribution are crucial, as they directly affect the quality of the mold and the final cast product. The mold is designed to withstand the temperature of the molten metal, usually between 1,000°C to 1,600°C, depending on the type of metal being cast.
Next, the pattern is introduced. A pattern is a replica of the final product, which is placed in the sand to create the impression that will form the cavity for the molten metal. Often made of wood, metal, or plastic, the pattern must account for shrinkage, as metals tend to contract as they cool. Proper design and dimensional accuracy are essential to ensure that the final casting meets specifications.
foundry sand casting process
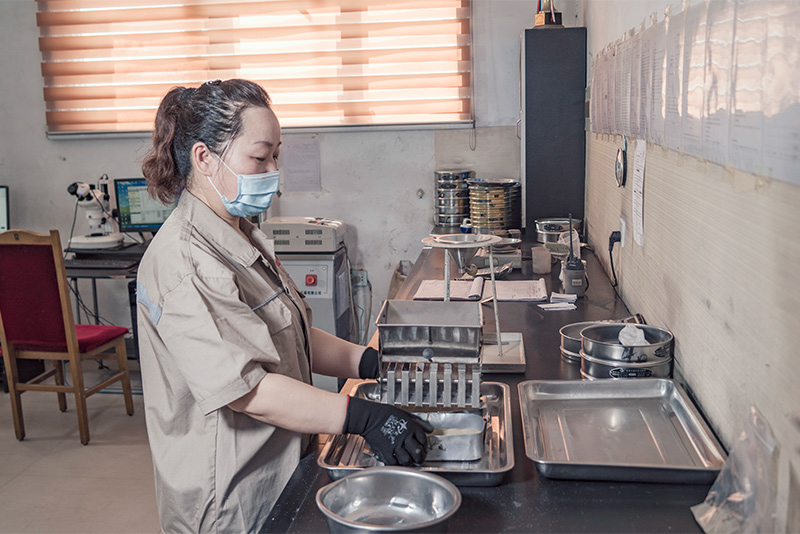
Once the mold is prepared and the pattern removed, it's time to pour the molten metal. This stage requires careful control of the metal's temperature and pouring speed to prevent defects like cold shuts, air pockets, and inclusions. The molten metal fills the cavity of the mold before it begins to solidify. Cooling time varies based on the metal type and thickness of the casting, but proper cooling is critical for achieving the desired mechanical properties in the final product.
After the metal has solidified, the mold is broken away to reveal the casting. This process includes shaking out the sand, which is often reused in the production of new molds. The casting may then require further processing, such as trimming, grinding, or machining, to achieve the final dimensions and surface finish.
Sand casting is favored for its flexibility and cost-effectiveness, especially for small to medium production runs. While it may not produce the same surface finish or dimensional tolerances as more advanced methods, its simplicity and adaptability make it a preferred choice for many engineers and manufacturers. In conclusion, the foundry sand casting process remains a pivotal technique in modern manufacturing, facilitating the production of a wide array of metal components.
Post time:10 月 . 18, 2024 19:15
Next:Innovative Techniques in Low Pressure Sand Casting for Enhanced Metal Forming Processes