The Foundry Sand Casting Process An Overview
The foundry sand casting process is a time-honored manufacturing technique that has been widely utilized in various industries for producing metal components. This method relies on the use of sand as the primary mold material, allowing for the creation of complex shapes with excellent dimensional accuracy and surface finish. In this article, we will delve into the essential steps, benefits, and applications of the sand casting process.
At its core, sand casting involves several key steps pattern making, molding, melting, pouring, solidification, and finishing. The process begins with the creation of a pattern, which is a replica of the final product to be cast. This pattern can be made from various materials, including wood, metal, or plastic, depending on the required precision and production volume. The pattern is then coated with a release agent to facilitate its easy removal from the mold.
Next, the molding phase commences. A mixture of sand and a binding agent, often clay, is compacted around the pattern to form the mold. The sand used in this process is typically silica sand, known for its high melting point and excellent structural properties. Once the mold is formed, it is carefully removed from the pattern, creating a hollow cavity that reflects the shape of the desired component.
Subsequently, metal is melted in a furnace to prepare for pouring. The choice of metal can vary widely, including aluminum, cast iron, bronze, and various alloys, depending on the specifications of the component. The molten metal is then poured into the mold cavity through a designated pour hole, and it fills the space, taking the shape of the mold.
foundry sand casting process
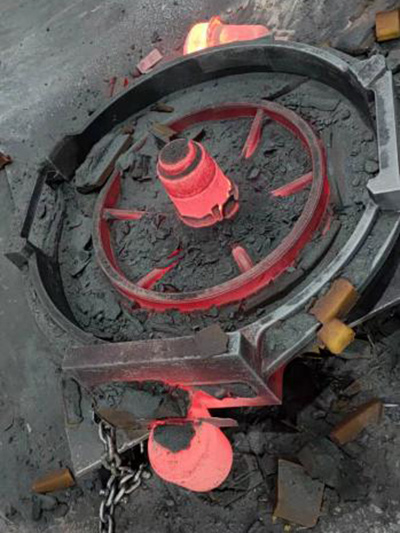
Once the metal has been poured, it undergoes solidification. As the molten metal cools, it transforms back into a solid state. This cooling process can be influenced by several factors, including the type of metal, the thickness of the components, and the properties of the sand. After sufficient time has passed for solidification, the mold is broken away, revealing the newly cast part.
The final step in the sand casting process is finishing. This can involve several operations, such as trimming excess material, machining for precision, sandblasting for surface smoothness, and any necessary heat treatments to enhance the properties of the final product. The end result is a high-quality metal component that meets the required specifications.
One of the key advantages of sand casting is its versatility. It can produce complex parts in a wide range of sizes and shapes, making it suitable for both small-scale and large-scale production. Additionally, the use of sand as a mold material is cost-effective and allows for easy recycling of used sand, aligning the process with sustainable practices.
The sand casting process finds wide applicability across various industries, including automotive, aerospace, construction, and artistic applications. Components such as engine blocks, gears, and various machinery parts are frequently manufactured using this method due to its ability to deliver robust and reliable products.
In conclusion, the foundry sand casting process is a vital technique in modern manufacturing that combines tradition with innovation. Its numerous benefits and adaptability make it an enduring choice for producing high-quality metal components across diverse applications. As industries continue to evolve, the significance of sand casting will undoubtedly remain prominent in the realm of metalworking.
Post time:10 月 . 03, 2024 13:39
Next:Kayıp Köpük Döküm Malzemeleri ve Uygulama Alanları Hakkında Bilgiler