Understanding the Differences Between Die Casting and Sand Casting
Casting is a fundamental manufacturing process where liquid material is poured into a mold to create a desired shape. Among the various casting methods available, die casting and sand casting are two of the most widely used techniques, each with its own unique characteristics, advantages, and applications. This article delves into the key differences between die casting and sand casting, exploring their processes, materials, applications, and overall advantages.
Casting Processes An Overview
Die casting is a fast and efficient process primarily used for producing small to medium-sized metal parts, particularly from non-ferrous materials such as aluminum, zinc, and magnesium. This process involves forcing molten metal into a mold (die) under high pressure. The molds used in die casting are typically made from hardened steel, which allows for high precision and excellent surface finish. The quick cooling and solidification of the molten metal yield parts with intricate details and dimensional accuracy.
On the other hand, sand casting involves creating a mold using a mixture of sand, clay, and water. The sand mold is typically created in two halves, which are then assembled to form a cavity. Molten metal is poured into this mold, where it cools and solidifies before the mold is broken away to reveal the casting. Sand casting is a versatile method capable of accommodating large parts, and it can work with a wide array of materials, including ferrous and non-ferrous metals.
Materials and Equipment
The materials used in both casting methods are a significant differentiating factor. Die casting predominantly employs non-ferrous metals, particularly those with low melting points, which can be rapidly processed and cooled. The equipment required for die casting can be quite sophisticated, involving hydraulic or pneumatic systems to achieve the necessary pressure for injecting the molten metal.
Conversely, sand casting can utilize a broader range of materials, including both ferrous (iron and steel) and non-ferrous metals. The equipment needed for sand casting is generally less complex and less costly. It often requires a pattern (the replica of the desired part), a sand mixer, and a furnace for melting the metal.
difference between die casting and sand casting
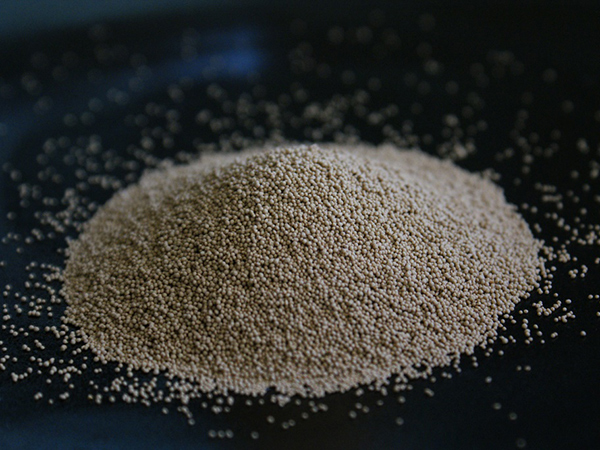
Surface Finish and Tolerances
Die casting offers superior surface finish and dimensional tolerances compared to sand casting. The high pressure used in die casting produces parts with smooth surfaces and fine details, making it suitable for applications where aesthetics and precise dimensions are crucial. Typically, die-cast parts require little to no machining after casting, which can significantly reduce production time and costs.
In contrast, sand casting tends to produce rougher surfaces and may require more extensive machining to achieve the desired finish and tolerances. The quality of the surface finish in sand casting is dependent on the sand used and the quality of the mold making process. While sand casting allows for rougher finishes, it provides more flexibility in creating larger parts.
Production Volume and Cost Considerations
When it comes to production volume, die casting is best suited for high-volume manufacturing. Though the initial costs are higher due to the need for durable molds and sophisticated machinery, the long-term savings from reduced cycle times and minimal post-processing make it advantageous for mass production.
In contrast, sand casting is more adaptable for low to medium production volumes. The absence of high upfront costs related to mold creation makes it an attractive option for prototyping or custom parts. However, because sand casting is slower and often involves additional finishing processes, it can be less cost-effective for large-scale production.
Conclusion
In summary, both die casting and sand casting are essential techniques in the manufacturing world, each serving distinct purposes and applications. Die casting is preferred for high precision, high-volume production of non-ferrous parts, while sand casting excels in versatility and the ability to create larger components using various materials. Understanding these differences enables manufacturers to select the appropriate casting method that aligns with their production needs, budget constraints, and desired outcomes.
Post time:10 月 . 14, 2024 22:25
Next:sand casting alloys