Sand Casting An Overview of a Timeless Manufacturing Process
Sand casting, also known as sand mold casting, is one of the oldest and most versatile manufacturing processes used to create metal parts of intricate shapes and sizes. This method has been utilized for centuries, dating back to ancient civilizations, and remains a popular choice in modern manufacturing environments due to its adaptability and cost-effectiveness.
The Basics of Sand Casting
The sand casting process involves creating a mold from a mixture of sand, clay, and water. The primary material used is silica sand, which is known for its ability to withstand high temperatures. The process begins with the creation of a pattern, which is a replica of the final product. The pattern is typically made from metal, wood, or plastic, and is designed to translate into a mold.
Once the pattern is ready, the next step is to prepare the mold. The sand mixture is compacted around the pattern to form a cavity that reflects the shape of the final product. This is done using a variety of techniques, including hand molding or machine molding, depending on the complexity and volume of the casting.
After the mold is formed, the pattern is removed, leaving a cavity in the sand. This cavity is where the molten metal will be poured. The mold is then assembled, ensuring that all the pieces are securely in place. To facilitate the flow of molten metal, runners and risers may be added to the mold to direct the metal and allow for proper filling and venting.
Pouring the Metal
The next phase of the sand casting process is the pouring of the molten metal into the mold. The metal is typically heated in a furnace until it reaches a liquid state, achieving temperatures ranging from 660°C (1220°F) for aluminum to over 1400°C (2550°F) for iron. Once the metal is ready, it is poured into the mold cavity, where it fills the space left by the pattern.
As the metal cools, it solidifies and takes on the shape of the mold. This cooling process is crucial, as it influences the microstructure and mechanical properties of the final casting. After sufficient time has passed for the metal to solidify, the mold is broken apart, revealing the cast product. This casting may require further finishing processes such as grinding, machining, or painting to achieve the desired specifications.
describe sand casting
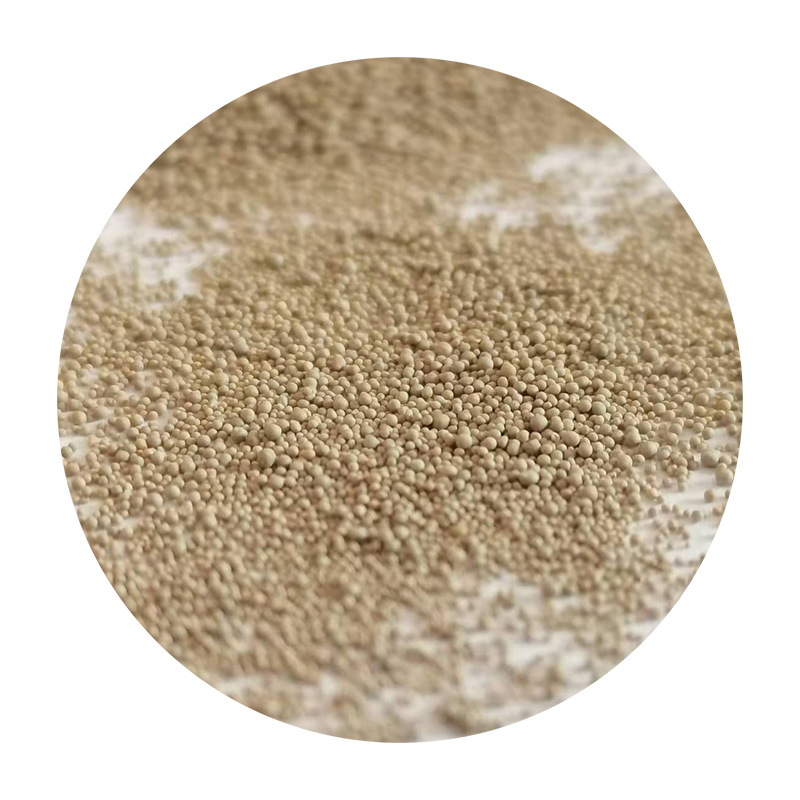
Advantages of Sand Casting
One of the primary advantages of sand casting is its adaptability to a wide range of materials, including ferrous and non-ferrous metals. This versatility makes it a preferred choice in various industries, including automotive, aerospace, and general manufacturing. Additionally, sand casting can produce large parts with intricate designs, which is often difficult to achieve with other casting methods.
Another benefit is the relatively low cost of materials and tools. Creating patterns and molds requires less investment compared to other methods, making sand casting an economical option for low to medium production volumes. Furthermore, the sand used in the process can be reused multiple times, reducing waste and contributing to sustainability.
Challenges and Considerations
Despite its many advantages, sand casting is not without its challenges. The process is subject to defects such as sand inclusions, cold shuts, and gas porosity, which can affect the quality of the final product. To mitigate these issues, careful control of the molding process, temperature, and metal quality is essential.
Moreover, the surface finish of sand castings may not be as smooth as those produced by other methods, potentially necessitating additional machining operations. As with any manufacturing process, thorough planning and skilled craftsmanship are crucial to achieving optimal results.
Conclusion
In summary, sand casting is a foundational manufacturing process that combines traditional techniques with modern applications. Its ability to produce complex shapes at a relatively low cost makes it invaluable in various industries. By understanding its principles, advantages, and challenges, manufacturers can effectively leverage sand casting to create high-quality components suited to their specific needs. As technology evolves, sand casting will undoubtedly continue to play a significant role in the world of manufacturing.
Post time:10 月 . 21, 2024 16:43
Next:High-Quality Metal Casting Sand Available for Purchase Online