The Role of Ceramsite Foundry Sand in Modern Casting Processes
In the world of foundry operations, the choice of materials significantly influences the quality and performance of cast products. Among various options available today, ceramsite foundry sand has garnered considerable attention for its unique properties and numerous advantages in casting processes. Composed largely of recycled materials, ceramsite sand blends sustainability with superior performance, making it an increasingly popular choice in modern foundry applications.
What is Ceramsite Foundry Sand?
Ceramsite foundry sand is a manufactured sand that is formed by the high-temperature processing of clay and other natural minerals. The end product is lightweight, porous, and spherical granules that exhibit a high level of thermal stability and resistance to high temperatures. This type of sand is particularly useful in metal casting as it possesses excellent flow characteristics and helps create finer surface finishes on cast products.
Advantages of Ceramsite Foundry Sand
1. Better Mold Integrity One of the standout characteristics of ceramsite foundry sand is its ability to maintain mold integrity at high temperatures. Its thermal stability means it can withstand intense heat without breaking down, ensuring that the shape and detail of the molds are preserved during the casting process. This leads to reduced defects and improved quality in the final products.
2. Sustainability In an era where environmental considerations are paramount, ceramsite sand stands out for its sustainability. Being made from recycled materials, it reduces waste and promotes the circular economy. Its production process is also less energy-intensive compared to traditional sand mining, leading to a smaller ecological footprint.
ceramsite foundry sand
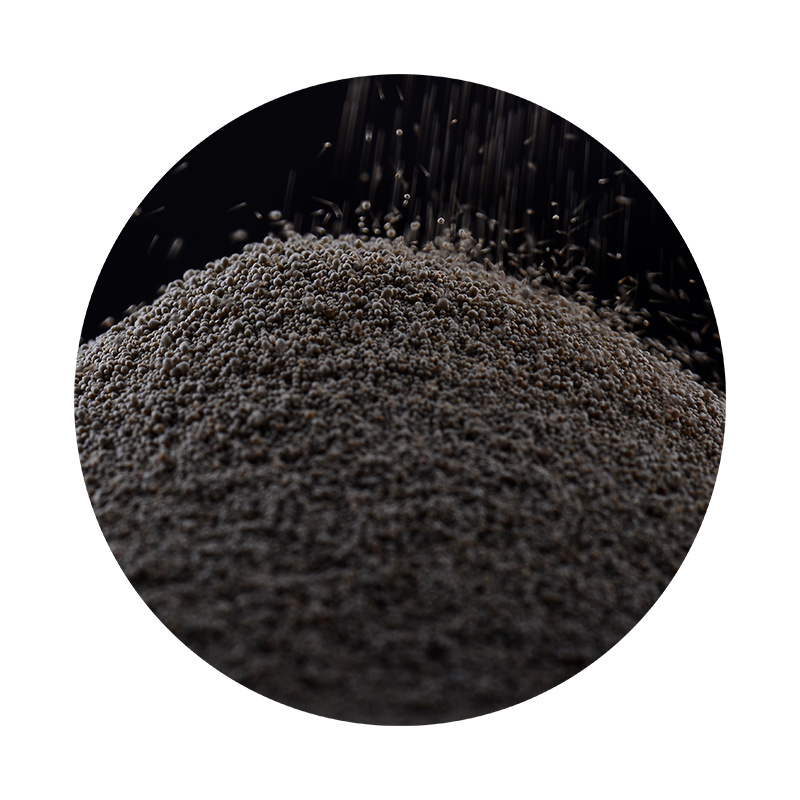
3. Improved Surface Finish The spherical shape and fine granulation of ceramsite sand contribute to superior mold filling capabilities. This results in improved surface finishes on cast products, reducing the need for extensive post-processing and polishing, which saves time and labor costs.
4. Enhanced Flowability The unique properties of ceramsite sand enable it to flow more readily than conventional foundry sands. This improved flowability allows for easier packing and molding, leading to more efficient production processes and the ability to create complex shapes with greater ease.
5. Versatility Ceramsite foundry sand can be utilized across a variety of metal casting processes, including sand casting, investment casting, and lost foam casting. Its adaptable nature means it can be employed in different alloys and casting techniques, making it a versatile option for many foundries.
Challenges and Considerations
Despite its numerous benefits, the adoption of ceramsite foundry sand is not without challenges. One significant hurdle is the cost associated with its production, which can be higher than that of traditional sand. Additionally, for foundries accustomed to conventional materials, transitioning to ceramsite sand may require adjustments in existing processes and practices.
Conclusion
Ceramsite foundry sand presents a compelling blend of performance, sustainability, and versatility that addresses many of the challenges faced by modern foundries. As industries continue to prioritize environmental responsibility and operational efficiency, the integration of ceramsite sand into casting processes is likely to grow. With its unique properties, ceramsite foundry sand not only enhances the quality of cast products but also contributes to a more sustainable future in metalworking and foundry operations. As innovations in material science continue to progress, ceramsite sand may well become a cornerstone of the green foundry movement, shaping the industry for years to come.
Post time:10 月 . 05, 2024 10:37
Next:Understanding the Definition and Uses of Foundry Sand in Metal Casting Industries