The Evolution and Impact of 3D Sand Printing in Casting
In recent years, the manufacturing industry has witnessed a revolutionary advancement in printing technology, notably the emergence of 3D sand printing. This cutting-edge method is reshaping the casting process, allowing for greater efficiency, design freedom, and sustainability. This article delves into the intricacies of 3D sand printing and its significant impact on casting applications.
What is 3D Sand Printing?
3D sand printing is a process that utilizes a digital model to create molds and cores for casting purposes. The technology employs a printer that layers fine grains of sand, binding them together using a chemical adhesive. This technology stands out for its ability to produce complex geometries that traditional methods cannot easily achieve. The sand molds created are often used for metal casting, where molten metal is poured into the mold to produce intricate components.
Advantages of 3D Sand Printing in Casting
1. Design Flexibility One of the most compelling benefits of 3D sand printing is the ability to manufacture complex designs without the constraints of traditional mold-making processes. Designers can create intricate patterns, lightweight structures, and geometries that were previously impossible or economically impractical to produce.
2. Reduced Lead Time Traditional casting techniques often require extensive tooling and setup time, which can delay production. In contrast, 3D sand printing significantly reduces lead times since the mold can be created directly from a computer-aided design (CAD) file. This expedites the prototyping phase and allows for rapid iterations to meet design requirements.
3. Material Efficiency The additive nature of 3D printing means that materials are used more efficiently. Less waste is generated compared to conventional methods, where substantial quantities of material can be discarded during the mold-making process. Additionally, the grains of sand used can often be recycled for future prints, promoting a more sustainable manufacturing process.
3d sand printing casting
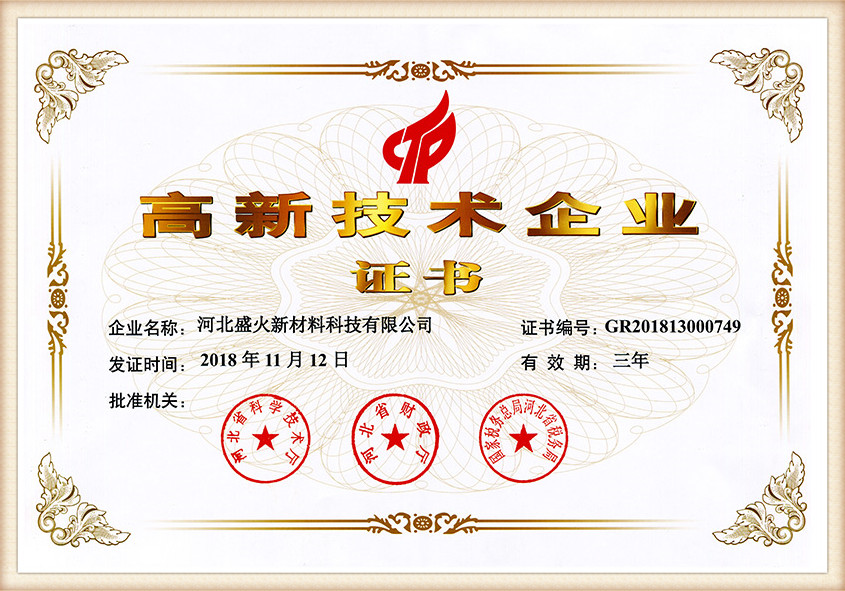
4. Customization The technology enables high levels of customization, allowing manufacturers to respond quickly to specific client requirements. Whether it's a single prototype or a production run of unique components, 3D sand printing makes it easier to adapt designs on-the-fly, fostering innovation and allowing for bespoke solutions.
Applications in Various Industries
The applications of 3D sand printing are wide-ranging and span across multiple industries. In the automotive sector, for instance, manufacturers use this technology to produce lightweight and intricate parts, contributing to overall vehicle efficiency. The aerospace industry benefits from 3D sand printed components as well, where weight and material optimization are crucial.
Moreover, the medical field is beginning to explore 3D sand printing for prosthetic devices and implants that require precise, customized shapes. The construction industry also sees potential in using 3D sand printing for creating molds for complex architectural features, leading to innovative designs in building facades and structural elements.
Future Prospects
As the technology matures, the future of 3D sand printing in casting looks promising. Continuous advancements in printer capabilities, material science, and software will likely expand the scope of applications further. Integration with other technologies, such as artificial intelligence and machine learning, could enhance the design process and further streamline production.
Conclusion
3D sand printing is not merely a trend but a transformative element in the realm of casting and manufacturing. It offers unparalleled flexibility, efficiency, and sustainability that traditional methods struggle to match. As industries increasingly recognize the value of this technology, it's expected that 3D sand printing will play a pivotal role in shaping the future of manufacturing, paving the way for more innovative, economical, and environmentally friendly production processes. As we move forward, embracing these advancements will be key to remaining competitive in an ever-evolving landscape.
Post time:10 月 . 21, 2024 20:26
Next:Innovative Applications of 3D Printing in Sand-Based Construction Techniques